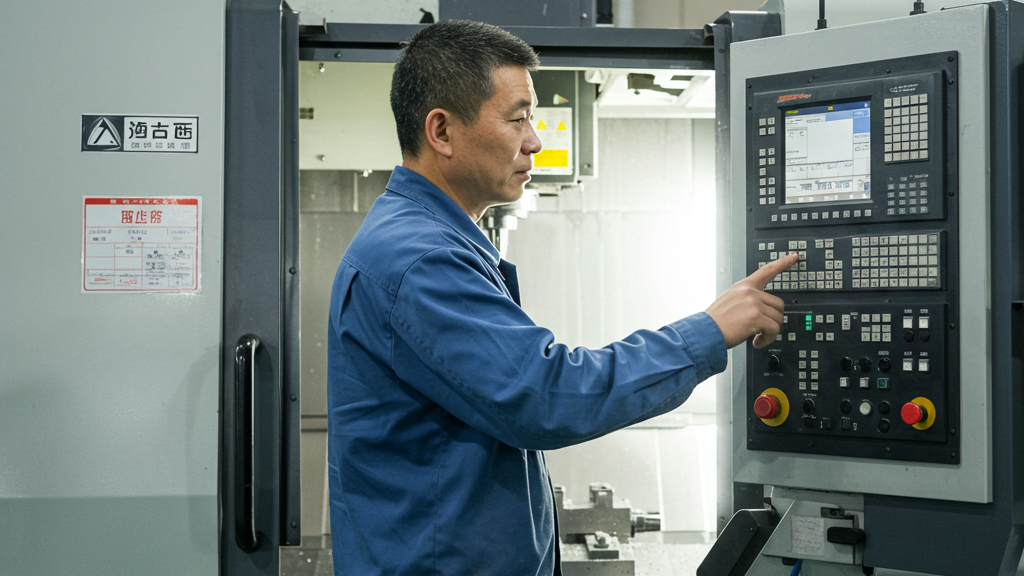
CNC precision machining plays a pivotal role in the manufacturing of complex parts. However, the issue of burrs appearing at fillets and chamfers poses a challenging problem, subtly affecting assembly precision, part functionality, and the overall aesthetic appeal of the product. The occurrence of burrs is not insurmountable; they are intricately linked to various factors such as process parameters, tool condition, and material properties. Relying solely on subsequent deburring processes is insufficient; the real key lies in cleverly integrating burr prevention measures into all aspects of the machining process.
This article will, from a professional perspective, thoroughly analyze the common causes of burr formation at fillets and chamfers in CNC machining. Simultaneously, it will focus on aspects such as tool selection, optimization of cutting parameters, meticulous planning of machining paths, and rational fixture design. It will also elaborate on corresponding avoidance strategies and technical key points to help improve machining quality and effectively solve the practical problem of burrs that plagues the machining field.
How are Burrs Formed on Fillets and Chamfers?
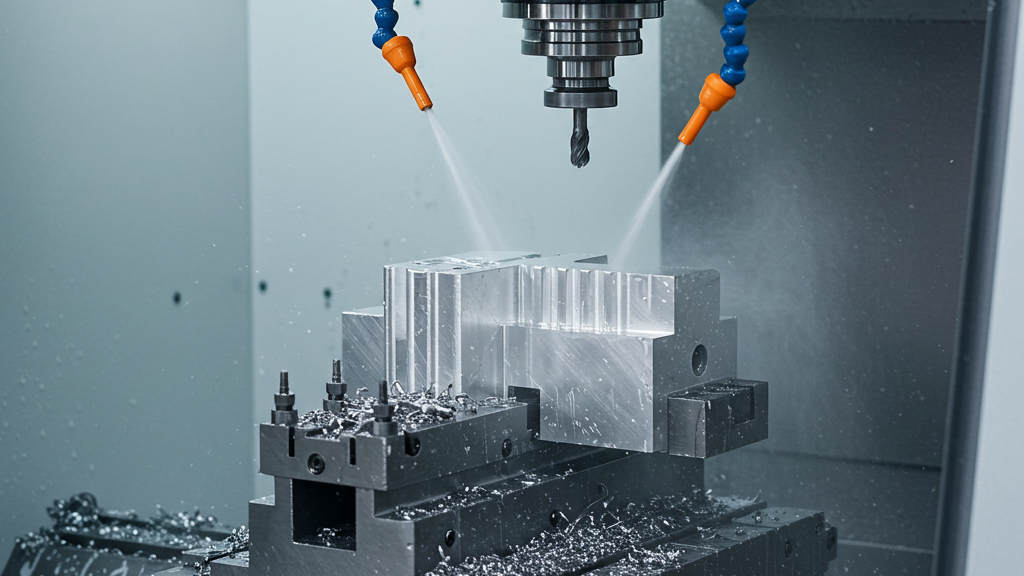
The formation of burrs during CNC machining of fillets and chamfers is a manifestation of the complexity of the material removal mechanism, stemming from the interaction of cutting forces, material properties, and tool conditions. A deep understanding of how these factors lead to unintended material deformation and fracture is crucial for effective burr control.
- Material Extrusion and Tearing: When the plastic deformation of the material exceeds its fracture limit, the edge material is extruded and torn, forming burrs.
- Poisson’s Effect and Lateral Extrusion: Lateral expansion of the material under pressure leaves residue at the cutting exit, resulting in burrs.
- Tool Wear and Unstable Cutting: A dull tool increases cutting forces and unstable cutting, leading to irregular material deformation and fracture, which generates burrs.
- Chip Formation and Accumulation: Poor chip control and evacuation cause chip accumulation and scratching, leading to burr formation.
How Can Tools and Parameters Prevent Burrs?
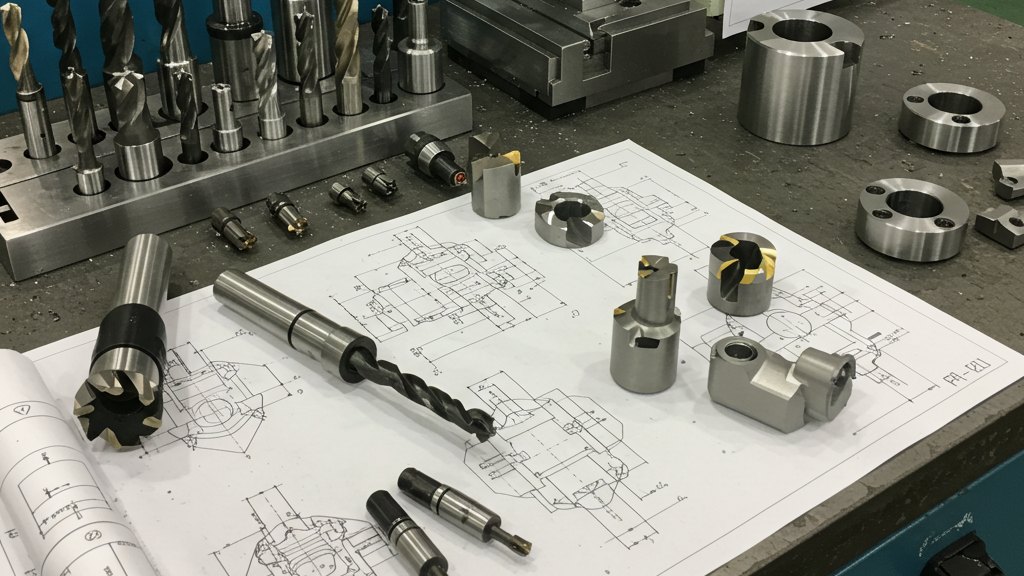

Addressing the root causes of burr formation during CNC machining of fillets and chamfers, precise tool selection and rational optimization of cutting parameters are at the heart of prevention strategies. By controlling the force state and material deformation methods during the cutting process, the likelihood of burr formation can be significantly reduced, thereby improving machining quality and efficiency.
- Reduce Material Extrusion and Tearing: Sharp cutting tools and low feed rates can minimize material extrusion and tearing, reducing burr formation.
- Mitigate Poisson’s Effect and Lateral Extrusion: Small lead angles and shallow depths of cut can suppress lateral expansion of the material. (Lead angle is also known as Major Cutting Edge Angle)
- Stabilize the Cutting Process and Reduce Adverse Deformation: High-rigidity tools and reasonable parameters can stabilize cutting and reduce burrs.
- Optimize Chip Formation and Evacuation: Proper flute design and parameters facilitate chip removal, avoiding secondary scratching and burr generation.
Do Path and Clamping Affect Burrs?
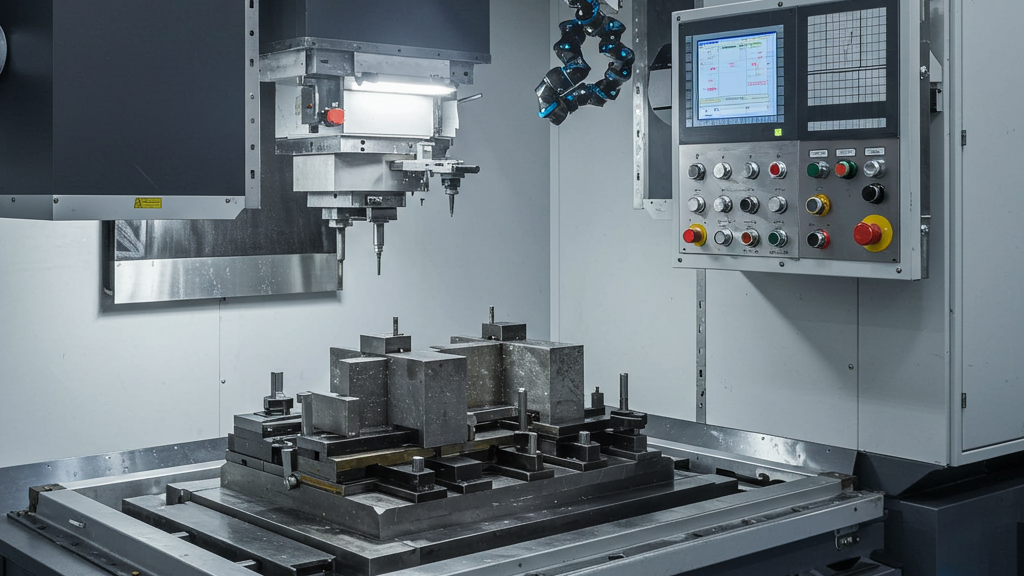
In addition to precise tool selection and optimized cutting parameters, reasonable machining path planning and stable workpiece clamping are also crucial steps in controlling burrs during CNC machining of fillets and chamfers. Careful path design can avoid sudden changes in cutting forces and unnecessary material accumulation, while stable clamping can effectively suppress vibrations during machining, providing a solid guarantee for high-quality, burr-free machining.
- Optimize Tool Entry and Exit: Using smooth entry and exit movements can reduce edge impact and tearing.
- Control Cutting Direction and Overlap: Maintaining a consistent cutting direction and using small, multiple cutting passes can smoothly remove material.
- Select a Suitable Machining Sequence: A reasonable arrangement of the machining sequence can provide better support for fillets and chamfers.
- Ensure Rigidity and Stability of Workpiece Clamping: Stable clamping can effectively prevent machining vibrations and displacement.
Key factors and countermeasures of CNC fillet chamfering burr
Prevention Category |
Key Strategies |
Specific Effects on Burr Prevention |
Tool Selection | Use sharp tools with positive rake angles and optimal geometry | Cuts material cleanly, reduces material squeezing and tearing |
Cutting Parameter Optimization | Lower feed rate, reduce cutting depth, select appropriate cutting speed | Reduces deformation in the cutting zone, inhibits lateral extrusion, maintains cutting stability, optimizes chip formation |
Machining Path Planning | Employ arc-in and arc-out approaches, maintain consistent cutting direction, optimize overlap | Reduces edge impact, avoids sudden changes in cutting force, ensures smooth material removal |
Workpiece Clamping | Use rigid fixtures, ensure multi-point support or specialized fixtures | Prevents vibration and displacement during machining, provides a stable machining environment |
Experienced Tips for Avoiding Burrs
In actual production, avoiding burr formation during CNC machining of fillets and chamfers is not only dependent on theoretical parameters; empirical techniques and best practices are equally important. These seemingly minor operations often contain a wealth of practical experience, and are key to improving machining quality and reducing post-processing costs.
1.Precise Cooling: Fine-tuning the coolant flow can effectively remove chips and cool the cutting zone, reducing thermally induced burrs.
2.Peck/Oscillation Machining: Using peck or oscillation machining facilitates chip breaking and evacuation, preventing chip accumulation and extrusion that can lead to burr formation.
3.Leave a Finishing Allowance: Leaving a finishing allowance and using multiple light cuts can reduce cutting impact, resulting in a smoother, burr-free surface.
4.Material-Specific Optimization: Optimizing tools and processes for specific materials is an effective way to avoid burrs.
Conclusion
Avoiding burr formation during CNC machining of fillets and chamfers is a systematic undertaking involving tool selection, cutting parameter optimization, machining path planning, workpiece clamping, and practical operational experience. Only by combining theoretical knowledge with practical experience, and continuously exploring and refining machining processes, can the burrs generated during CNC machining of fillets and chamfers be effectively reduced or even eliminated, ultimately improving the machining quality and production efficiency of the parts.
For expert assistance in implementing for your production needs, visit our resource center or contact us. Let’s help you scale up your manufacturing with precision and efficiency!
Post time: Apr-23-2025